Storable noxious gasses are made available in cylinders equipped with the appropriate fittings. It could be the case that, for certain tests, thinned gasses or mixed gasses must be dosed instead of concentrated gasses. Gasses that cannot be stored (e.g. ozone), are produced within the system itself.
Temperature and humidity are maintained within specified tolerance limits in the chamber. The test room is not imposed to corrosive gases. The chamber inside is exposed to corrosive gases given through pneumatic cylinders. The perforated floor of the chamber ensures equal distribution of gas. The nature of the materials are studied under corrosive gases given according to standards by the user. The required concentration is calculated by ration of noxious gas volume flow to that of air volume flow.
Weiber noxious gas test chambers are double walled convection heated and cooled units. Outer body of our environmental chambers are constructed out of thick PCRC, pre coated corrosion resistant GI sheet duly pre-treated with primers and rust proofing and painted with long lasting stove enamel or elegantly powder coated. The inner chamber is made of heavy gauge stainless steel sheet of SS-304 grade). The gap between the walls is filled high grade mineral glass wool, which ensures maximum thermal efficiency in our chambers.
The unit is provided with single door. This door is provided with magnetic door closer. This door is provided with lock and key arrangement. The unit is mounted on a sturdy steel frame. The unit is provided with various customized shelves in various permutations and combinations to suit individual requirements. The triple walled back of our noxious gas test chambers are provided with two/Four/Six/Eight (size specific) air circulation fans for uniform maintenance of the temperature throughout the chamber.
HMI+ PLC IN ONE UNIT:
Weiber provides better automatic controls for the chamber by integrating HMI and PLC together. This special feature is compelling alternative to traditional methods and provides a simplified, reduced cost control system architecture.
It works by following operating steps:
- Sensors measure the physical quantity like temperature and convert them to electrical signal
- The actuation device acts upon that electrical signal
- At HMI interface between operator and chamber occurs.
- The machine operates with the logic design controls controlled by software.
- This signal is sent to the chamber by logic control devices and the chamber operates.
Basic features of HMI+PLC:
- Processor of 1.6 GHz: High clock speed processing PLC that enables speed up processing to the functions. With 1.6GHz processing speed, the PLC system is capable of multitasking, processing of large data volume, and high performance.
- Audio Output Alarm: Audio alarm alertin case of failures in any of the component controlling functions.
- 256 MB of RAM: PLC of 256Mega Byte memory for running programmes offers high memory space for installing of more programs
- COM Port: Com port provided for attaching RS 235/RS 485 cable.
Increased Numbers of On - Board I/O peripherals (10-50): Maximum number of 50 I/O peripherals provided on request, to attach input and output devices to the HMI and PLC. Increased number of input and output peripherals allows adding of devices like printers, recorders, etc.,as per the need.
Data Logging and Free Pprogramming Software: Attached data logger with input program software provided. Through data logging software, HMI and PLC collect datathrough sensors, analyse the data and save and output the results of the collection and analysis. Examples of the types of information a data logging system can collect include temperatures, sound frequencies, vibrations, times, light intensities, electrical currents, pressure and changes in states of matter.
CoDeSys (Controller Development System) software technology
Heating:
Indirect heating system is provided in our units, comprising of air heaters made of high grade Kanthal A-1 wires of suitable wattage. The warm air is evenly distributed throughout the chamber through efficient motor fans ensuring very good temperature sensitivity.
Cooling:
An energy efficient cooling unit is installed in our photostabilitytest chambers to enable studies at lower room temperatures. We use high end CFC free compressors of Kirloskar/Tecumseh / Bitzer/ Denfos make, conforming to latest international standards and guidelines.
DETAILED DESCRIPTION ALONG WITH SALIENT FEATURES ARE AS UNDER FOR REFRIGERATION MACHINE
CONDENSING UNIT
AIR-COOLED CONDENSOR
Air-cooled condenser is internally grooved finned copper tubes used for high heat transfer area, which not only reduce power consumption, but also bring down the condensation faster. This unit is designed. &verdigris& reduces the resistance, saves energy consumption and ensure good heat exchange.
COMPRESSOR:
- HERMETIC COMPRESSOR
Single stage Reciprocating Compressor. Give the High Efficiency compared to sealed compressors, Less Power Consumption , Accessible for repairing, low noise level, Less Vibrations, Wide Voltage Range, Designed for Extremely High Ambient ,Full warranty etc
- COOLING SYSTEM
The compressor is mounted perfectly to ensure recommended level of sound and vibration.
REFRIGERATION CONTROL
- Low and High Pressure switch of RANCO/Danfoss
Which ensures the compressor and refrigeration system when low pressure will occurs it trip off the compressor. This is the only operator friendly switch can easily reset.
- Hand Shut off Valve
Is the only Condensing Unit, which is equipped with it. This valve is used for pump down the total gas in to the condenser & receiver in the faulty condition.
- Liquid Dryer of Danfoss make
Which is equipped in the liquid line for ministration of moisture in the liquid. It will collect all the moisture in side the refrigeration line as well as gas.
- Moisture Indicator of Danfoss make
The sight glass area in the Moisture Indicator shows at a glance the condition of the refrigerant system. The moisture indicator element changes colour and indicate if the system is safely dry, or dangerously wet.
- Solenoid Valve of Castle make
In most refrigeration applications, in order to automatically control the flow of fluids in a system, it is necessary to be able to start or stop the flow in the refrigerant circuit. An electrically operated solenoid valve is usually used for this purpose. Its basic function is the same as a manually operated shutoff valve, but it can be positioned in remote locations, and may be conveniently controlled by simple electrical switches.
- Oil Separator of Stainless Steel 304
The oil separator intercepts the oil mixed with compressed gas and returns it into the crankcase of the compressor, thus assuring an efficient lubrication of its moving parts. Also, it improves the overall efficiency in the system.
- Suction Accumulator
Maximum Efficiency of the relief device (expansion valve) because it is supplied with sub cooled Liquid.
- Liquid Receiver
As per ASME Section VIII Division I for storage of refrigerant.
Humidity Range
20% to 85%RH
Humidification (WATER TANK AND AEROSOL SYSTEM)
A low-pressure droplet free vapour boiler using direct vaporization system is used. Water Reservoir is provided at the side of the chamber with a 10 x 8mm PU tube quick connector and water level is automatically controlled through a water-in solenoid valve. The wick tank water level is automatically maintained through a water solenoid valve and an electrical float switch. The de-mineralized water or single distilled water supply to the humidity inlet having a resistance measurement of approximately 50,000 – 200,000 Ohm/cm is provided with the unit
Aerosol Generator and Monitor is a multi-function aerosol instrument comprised of an atomizer aerosol generator. As an aerosol generator can be used to generate a monodisperse aerosol by atomization. The output aerosol concentration is continuously monitored by control facility to provide a stable aerosol output with a known particle size and a known aerosol concentration from 10nm to1000nm. Water Reservoir is provided at the side of the chamber with a 10 x 8mm PU tube quick connector and water level is automatically controlled through a water-in solenoid valve. The wick tank water level is automatically maintained through a water solenoid valve and an electrical float switch. The de-mineralized water or single distilled water supply to the humidity inlet having a resistance measurement of approximately 50,000 – 200,000 Ohm/cm is provided with the unit.
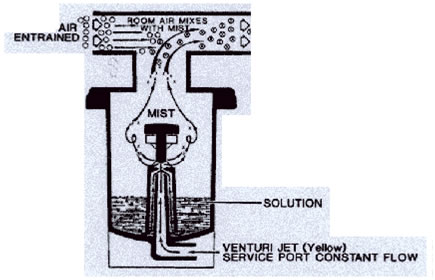
- Dehumidification: Refrigeration based de-humidification system is used. The desired level of lower humidity will be achieved by maintaining the precise dew point temperature. If you need more low humidity than the standard range then refrigeration based dehumidification system can be incorporated on customer’s request.
- Humidity Sensitivity: Humidity is controlled by mean of an electronic humidity controller cum indicator with an accuracy of ±3%RH
- Temperature Control: The temperature inside our temperature and humidity controltest chambers is controlled through Nano technology based HMI & PLC controller.
- Temperature Range: Temperature range of our standard Chamber is -2°C to +40°C. . However we have the capacity to modify the same to suit the individual specialized requirements of our customers.
- Temperature Sensitivity: Temperature inside our Temperature And Humidity Control test chambers are controlled with a sensitivity of + 0.3 o C or better.
- Illumination: OurTemperature and Humidity Control test chambersare provided with door operated illumination system comprising of fluorescent lights, beside two panels of diffused fluorescent light panel located at the either side of the chamber to enable the user to conduct the photo periodic tests and experiments.
- Insulation: The gap of 75 mm between the outer and the inner wall is filled with special grade glass wool to prevent thermal losses.
- Mineral Glass Wool Insulation: Glass mineral wool is one of the most environmentally friendly, stable and sustainable insulates available. Glass wool is incombustible by nature. Euro class classification is A. It does not propagate flames and toxic smokes. Thanks to a dense entanglement of materials with a low conduction and trapping a great amount of air, glass wool is an excellent thermal insulant. The thickest it is, the best thermal resistance it has, thus reducing heat losses in our equipment’s for better sensitivity and economical operations. And its impact on the environment in manufacture, use and disposal is minimal.
- Air Circulation: Triple walled back of unit is fitted with two air circulation fans for maintaining temperature uniformly throughout the chamber
Features of Coaxial Circulation Fan:
- Vacuum impregnated stator winding with dr. back varnish under red baktol
- Non-hygroscopic.
- Best IR value
- Bright bar (EN - 8 class) shaft.
- Bush bearing of branded companies.
- Surge comparison testing in fans and pumps eliminates into turn short circulating of the stator.
- Pressure die-casted-rotor manufactured with zero error.
- Boats of high accuracy
Port hole: port holes with silicon enclosure is provided at back side of the chamber. Through the port hole you can input sensors, wires and other test equipment. Silicone foam plugs have excellent temperature and humidity resistance and offer very good thermal insulation. Generally a single port hole is given but more numbers ca be increased according to customers request.